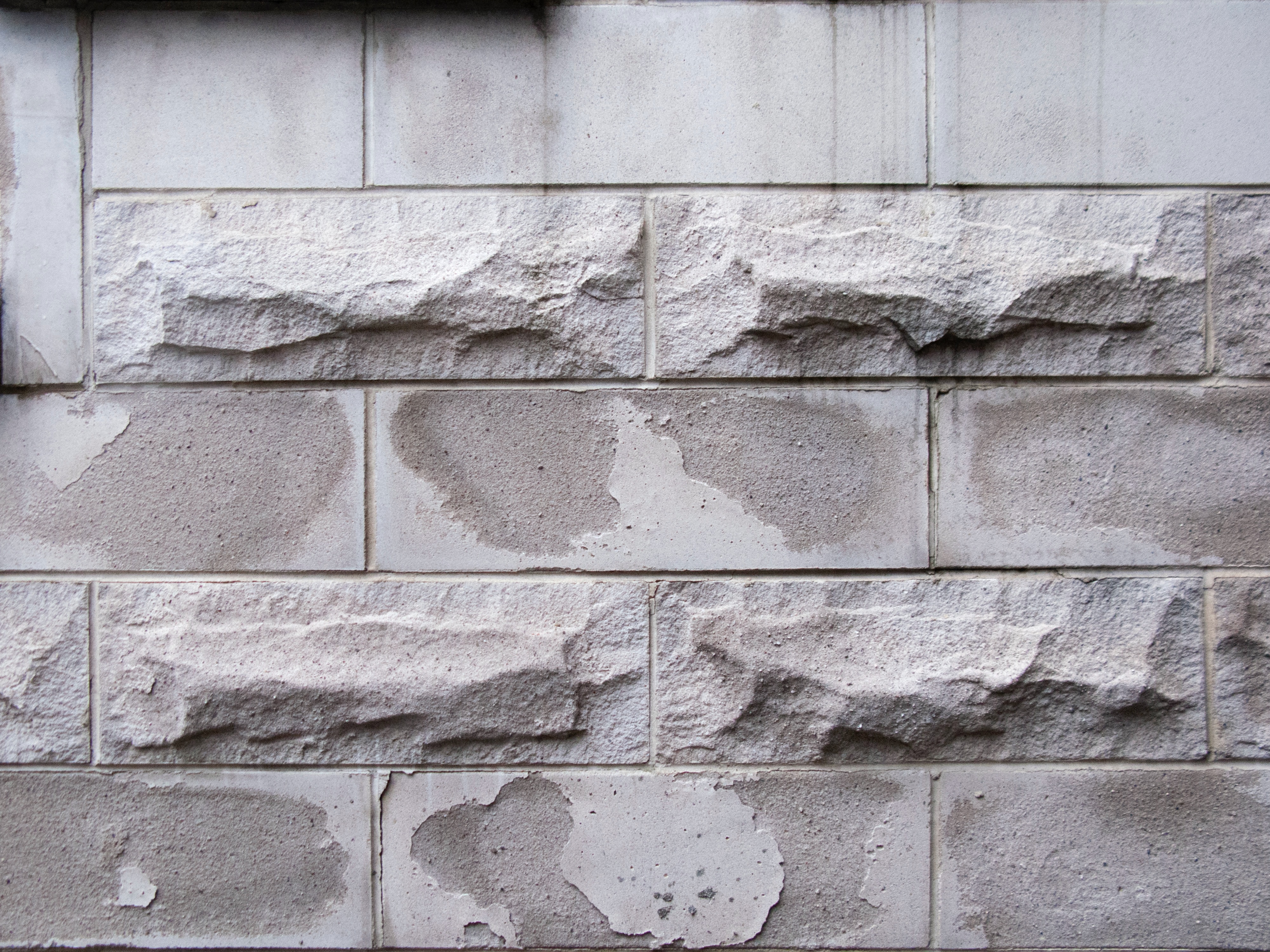
Производство цемента имеет огромное значение для каждой страны мира — цемент и бетон являются самым употребляемым в экономике ресурсом после воды.
Цементная промышленность имеет ключевое значение для экономического развития всех стран, поскольку динамика ее роста является во многом определяющей для развития национальных экономик. В настоящее время отрасль демонстрирует опережающее развитие, темпы роста которой превышают показатели изменения мирового ВВП.
01 Виды цемента
Клинкер — продукт равномерного обжига до спекания однородной искусственной сырьевой смеси, состоящей из известняка и глины определённого состава, обеспечивающего преобладание силикатов кальция (3СаО∙SiO2 и 2СаО∙SiO2 70-80%).
02 Способы производства портландцемента
При измельчении клинкера вводят добавки: от 1,5 до 3,5% гипса СaSO4∙2H2O (в перерасчёте на ангидрид серной кислоты SO3) для регулирования сроков схватывания и до 15% активных минеральных добавок для улучшения физических свойств цемента (водостойкий, морозостойкий, быстротвердеющий и т.п.) и снижения стоимости цемента.
03 Сырьё для производства портландцемента
04 Мокрый способ изготовления портландцемента
05 Обжиг сырьевой смеси
Основной тенденцией технического развития цементной промышленности в России и мире является сокращение производственных мощностей, работающих по «мокрому» способу и переход на технологию «сухого» производства. Эту тенденцию подтверждают также опыт мировой цементной промышленности по внедрению печных систем с реактором-декарбонизатором различных типов, которыми оснащаются новые и реконструируемые цементные заводы.
Доля выпуска цемента по сухому способу составляет в Японии, Испании и Германии — 100%, Италии — 96%, США — более 60%, в странах Европы 75-97%.
На данный момент в России активно обсуждается тема модернизации действующих производств, которая признаётся фактически основным направлением развития российской экономики.
Большинство заводов в Российской Федерации работает по мокрому способу производства, т.к. основная часть цементных заводов в России была построена во времена СССР, в период с 1950-х по 1980-е годы. Себестоимость производства цемента на таких устаревших линиях весьма велика и в большинстве случаев требуется их реконструкция и модернизация, с заменой устаревших печей, которая приведет к экономии топливо-экономических ресурсов и соблюдению жестких экологических требований.
Необходимость модернизации особенно очевидна на примере цементной отрасли: наибольшая доля цемента (87 %) в нашей стране производится по «мокрому способу», когда поступающее в обжиговую печь сырье имеет высокую влажность, которая неизбежно приводит к повышенному энергопотреблению и, соответственно, большому объему вредных выбросов в атмосферу.
Компания SEVERIN DEVELOPMENT принимала участие в проекте модернизации одного из крупнейших и старейших цементных заводов РФ — Вольского цементного завода, восьмого завода Российской империи, который был построен в 1897 году.
Проект «Волга» с модернизированной производственной линией стал одним из крупнейших в цементной отрасли страны за последнее десятилетие. Завод, благодаря совместной работе LafargeHolcim и SEVERIN DEVELOPMENT, наладил выпуск продукции мирового уровня, соответствующей высочайшим стандартам качества и экологии. Чтобы возродить «Вольскцемент», одно из старейших предприятий России, понадобилось почти 300 млн евро инвестиций и четыре года работы, за время которых был достигнут рубеж в 5 млн человеко-часов.
01 Технологическая линия
Проект «Волга», в рамках которого установлена новая технологическая линия по производству клинкера «полумокрым» способом, представляет собой модернизацию участка подготовки сырья (шламовые бассейны) строительство новых пресс-фильтров, установку нового циклонного теплообменника и усовершенствование связанных с этим технологическим оборудованием инженерных и транспортных систем.
По мере выхода новой «полумокрой» линии на проектную мощность устаревшие печи, работающие по мокрому способу, будут постепенно выводиться из эксплуатации. Проект позволит на 30 % сократить расход топлива и резко снизить уровень вредных выбросов.
Благодаря современному высокоэффективному пылеулавливающему оборудованию достигнут минимальный объем выбросов пыли. В общей сложности на новой технологической линии установлено дополнительно 19 пылегазоочистных установок, в том числе большой рукавный фильтр на печи, рукавные фильтры меньшего размера на вспомогательном оборудовании, электрофильтр на клинкерном холодильнике.
02 Оборудование
При реализации проекта, применялись решения таких ведущих производителей оборудования для цементной промышленности, как FLSmidth, KHD HUMBOLDT Wedag, Christian Pfifer, Aumund и пр.
03 Сырьевая база
Сырьевая база Вольского завода позволяет производить высокопрочные цементы первой группы эффективности и сульфатостойкие цементы, которые востребованы на строительстве объектов транспортной инфраструктуры (мостов, тоннелей), в промышленном строительстве при возведении особо прочных железобетонных конструкций, работающих под высокими нагрузками.
Крупные отраслевые игроки есть и в других мировых регионах:
Крупнейшие производители цементов в мире — китайские промышленные конгломераты, которые занимают две трети от мирового производства цемента.
Лидеры отечественной цементной промышленности:
Входит в ТОП-10 мировых производителей цемента. В составе Группы 16 предприятий суммарной мощностью более 50 млн тонн цемента в год. Сибирский цемент
Владеет тремя заводами с годовой производственной мощностью выше 5 млн тонн цемента. Новоросцемент
В составе холдинга четыре предприятия, расположенных в районе Новороссийска. Компания занимает порядка 10% рынка отечественного цемента. Востокцемент
Три завода полного цикла, входящие в Группу, производят более 4 млн тонн цемента в год. LafargeHolcim
В активах компании было четыре завода производственной мощностью 8 млн тонн цемента. 14 декабря 2022 года компания объявила о продаже российского бизнеса менеджменту предприятий. Heidelberg
Под управление компании находятся три российских завода, производящих почти 5 млн тонн цемента в год. Востокцемент
Три завода полного цикла, входящие в Группу, производят более 4 млн тонн цемента в год. Dyckerhoff
Компания входит в международную Группу Buzzi Unicem, которая управляет предприятиями по производству цемента в 12 странах мира. В России у холдинга три завода общей мощностью порядка 6 млн тонн готовой продукции в год.
В России насчитывается порядка 60 заводов суммарной мощностью более 100 млн тонн в год. Львиная доля приходится на четыре крупнейших холдинга и три подразделения зарубежных производителей.
Независимые компании по производству цемента занимают лишь пятую долю рынка.
Если у вас остались вопросы, сообщите нам, и мы свяжемся с вами в ближайшее время